Characteristics Of Cylindrical Fabric Technology
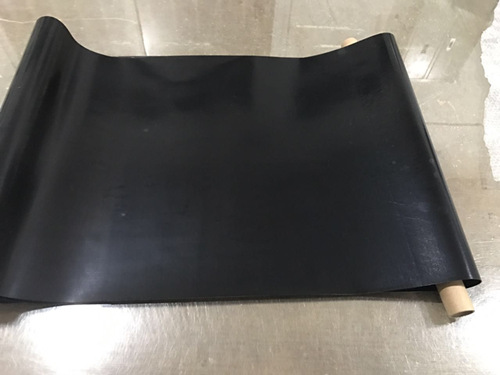
I. The characteristics of cylindrical fabric technology, the production of cylindrical fabric mainly has the following features:
1.When weaving cylindrical fabric, the warp yarns are divided into two non interfering systems on the same machine, forming the upper and lower layers of the fabric. The weft yarns are fed into the separate upper warp yarn shuttle and then into the lower warp yarn shuttle. This cycle forms a cylindrical fabric. The upper and lower layers of fabric are both plain weave. Figure 1 shows a transverse cross-section of a cylindrical fabric
A-Upper layer warp yarn,B-weft, C-Bottom layer warp yarn
2.In actual weaving, the warp density of cylindrical fabric is 120 strands/inch. When weaving the lower layer of fabric, 75% of the warp yarns are located at the top of the shuttle. The weft yarn is easily caught by the loose and dense upper warp yarn, causing warp to warp and weft to shrink. According to statistics, about 85% of weft shrinkage occurs on the switch side of the lower fabric. Weft shrinkage defects sometimes account for about 25.4% of total weaving defects.
3.Spiral cutting is used in the processing of cylindrical fabrics abroad, so it is required that the difference between the warp density at the edge of the fabric and its own warp density should not be too large, otherwise there will be stripe shadows at the original crease after printing and dyeing finishing.
4.The cylindrical fabric adopts a multi arm opening device for lifting, and coupled with the difficulty of clear opening, it is more prone to produce defects such as hundred feet and yarn sinking. It will cause the upper and lower layers of fabric to be twisted together, resulting in blockage inside the cylinder and causing major defects in the fabric for foreign users during processing and cutting.
5.When weaving cylindrical fabric, the weaving defects of the lower layer of fabric can only be seen clearly by the handyman when the fabric is rolled onto the wooden roller, making it difficult to control.
Due to the various production characteristics and factors mentioned above, the fabric has a high defect rate and production is relatively difficult. This article explores in depth how to control and solve quality problems based on the weaving characteristics of cylindrical fabrics.
II.Process measures
(1)Reasonably design the machine diagram
1.Organizational chart, pattern layout (shuttle direction)
When weaving the lower layer fabric, three warp yarns are on top and one warp yarn is on the bottom. The warp yarn on the upper sheet is both dense and loose, and the weft yarn is easily entangled by the warp yarn on the upper sheet during the insertion and beating process, causing weft shrinkage. When weaving the upper layer of fabric, only one warp yarn is on top and three warp yarns are on the bottom, resulting in less weft shrinkage. Therefore, it is required that the tension of the weft yarn in the shuttle should be relatively higher when weaving the lower layer of fabric.
Due to the fact that when the shuttle is stopped on the shuttle changing side, the length of the weft yarn drawn out by the shuttle (the distance from the fabric edge to the shuttle porcelain eye) is longer than when it is stopped on the switch side. In addition, the weft yarn on the shuttle changing side is easily stuck by the machine. When the shuttle is inserted into the shuttle opening from the shuttle changing side, the tension of the weft yarn is relatively small, and it is not easy to resist the reverse twisting potential energy of the weft yarn, resulting in dense weft shrinkage and a large number of them. In addition, when the cylindrical fabric is opened, the difference between the warp yarns of the upper and lower pieces is large each time, and the fabric surface at the opening bounces violently, and the warp density is high. Therefore, it is not suitable to use a point pecking type weft breaking self stopping device. When using the weft fork to probe the weft yarn, it is And it will also hold the weft yarn, causing it to unwind more when the shuttle is on the switch side. When it is on the shuttle changing side, the weft yarn is prone to spinning, At a distance of 8-18cm from the switch side fabric edge, there is a weft shrinkage (this distance is exactly the same as the distance from the fabric edge to the weft fork). In comparison, the tension of the weft yarn thrown out from the switch side is greater than that thrown out from the shuttle changing side. The comparison of the two directions of the shuttle when weaving the lower layer fabric and the weft shrinkage defects is shown in the table
From this, it can be seen that the number of weaving defects thrown out by the shuttle from the switch side during the weaving of the lower layer fabric is significantly less than that thrown out from the shuttle replacement side. Based on this situation, we have made necessary improvements to the design of the machine diagram, as shown in Figure 2
A-drafting plan;B-Reed diagram; C-shuttle changing side; D-switch side; E-bottom layer fabric warp yarn; F-upper layer fabric warp yarn; G-pattern layout
In Figure 2, X, The "mouth" represents the floating point of the lower and upper warp yarns respectively, and "O" represents the organizational point where the upper warp yarn floats above the shuttle mouth when the lower warp yarn is interwoven and does not participate in the interweaving.
2.Wearing patterns and reed patterns
The 4 warp yarns in the same group should be threaded in one reed tooth to facilitate overlapping of the warp yarns in the same group and reduce square holes. The chance of the warp yarn of the upper fabric floating on the top of the shuttle is 75%. It should be threaded through the back two pages of the warp frame to increase its opening tension and tighten the upper warp yarn, which can reduce weft shrinkage and weaving defects.